Table of Content
1 What is Design Verification and Validation?
2 Difference between verification and validation in FDA design
3 Design Verification & Design Validation for Medical Devices
4 Basics of Design Verification & Design Validation Process
5 Tips for Better Design Verification & Validation
6 Steps to Create effective design verification and validation plans
7 Concluding thoughts!
The Qualityze Advantage
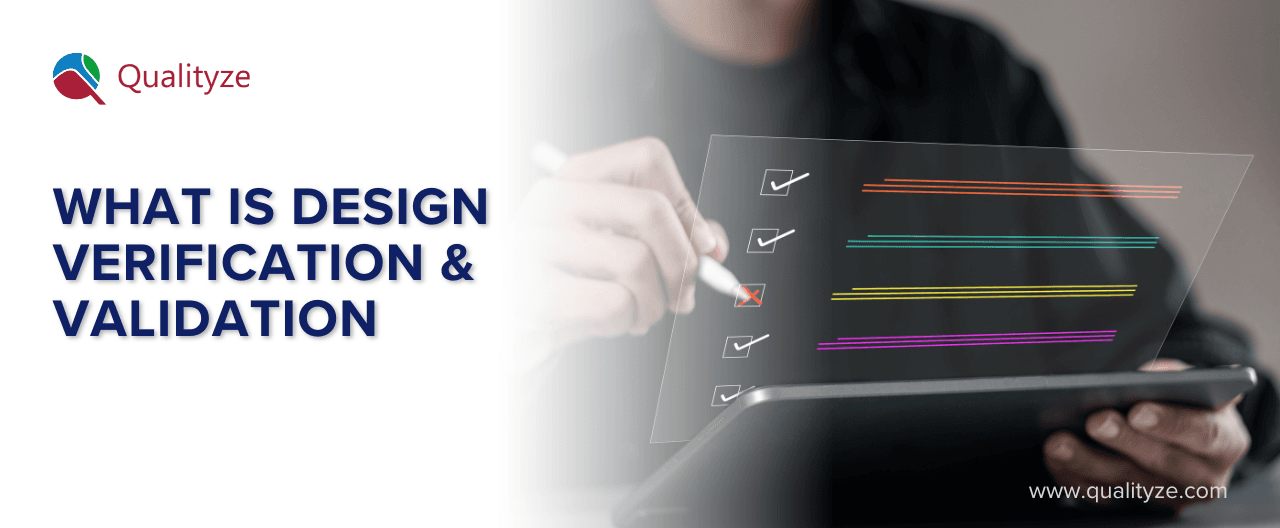
For medical device, pharma, or biotech companies, product design is not an engineering exercise, but a compliance journey. Design verification and validation (V&V) are the important milestones in the journey, basing your development strategy in both technical correctness and end-user safety.
These are not interchangeable steps. Verification questions, "Did we create the product to the design specs?" Validation takes a step further - "Does the product satisfy the needs of the user in real conditions?" FDA and ISO regulations clarify this difference, and so should your quality process.
Verification and validation no longer remain optional, but it's best practice in today's competitive and regulated business environment. A wrong move here can hold up regulatory clearances, add rework expenses, or lead to non-conformity.
This blog will dig into verification and validation from a quality management perspective—no nonsense, just practical insights. We’ll clarify what each process means, why they matter, and how Qualityze can help your organization keep regulators happy while ensuring your products are safe, reliable, and market-ready.
Let’s get right to it and unpack what design verification and validation really entail.
What is Design Verification and Validation?
Prior to jumping into technicalities, the fundamental purpose of design verification and validation in any regulated product development setting should be understood.
Design verification is a formal process to ensure that the design outputs are consistent with the design inputs. In other words, it checks that the product has been constructed correctly—to the specified documents. Verification activities are typically inspections, design reviews, simulations, and functional testing. They are repeatable and controlled processes that create conformance to stated requirements.
On the other hand, design validation answers the more user-centric question: Does the product fulfill its intended use in real-world conditions? The design validation process typically involves usability testing, clinical evaluation, pilot production, or field trials. It's conducted under actual or simulated operating conditions to ensure the product meets customer needs and regulatory expectations.
Together, verification and validation (V&V) act as a quality and risk management duo—ensuring both compliance and customer satisfaction before product release.
Whether you’re developing a mechanical assembly or a software-powered medical device, neglecting either of these processes can lead to failure in audits, product recalls, or worse—patient harm.
Let’s now explore how the FDA differentiates design verification vs validation and what this means for your compliance strategy.
Difference between verification and validation in FDA design
Understanding the difference between verification and validation in FDA design is critical for maintaining compliance and ensuring product safety. While often grouped together, they serve distinct roles in the design control process under 21 CFR Part 820.
Design verification confirms that the product design output meets the specified input requirements. It’s a question of conformance to intent—ensuring that every functional and performance specification is fulfilled. Common methods include inspections, tests, analyses, and demonstrations.
Design validation, on the other hand, ensures that the final product meets user needs and intended uses in real-world conditions. This involves actual product testing under expected usage scenarios—often including clinical evaluations or user feedback. It confirms fitness for purpose.
The FDA’s Quality System Regulation (QSR) outlines these steps clearly, emphasizing that both verification and validation are required—and must be well-documented—to avoid compliance risks during inspections or submissions.
Did you know? FDA 483 observations frequently cite improper validation of design controls. In fact, inadequate design validation remains one of the top 5 reasons for medical device recalls.
Next, we explore how verification and validation are specifically applied in the medical device industry—where precision is non-negotiable.
Design Verification & Design Validation for Medical Devices
In regulatory product development, particularly medical devices, the distinction between design verification and validation forms the foundation of compliant design practices. While both are components of FDA design controls, they serve entirely different purposes within a product's lifecycle.
Verification is all about conformance. It involves confirming that the design outputs meet the initial design input specifications. Think of it as confirming whether the blueprint was followed correctly using tools like functional testing, inspections, and statistical analysis.
On the other hand, validation is centered on suitability. It determines whether the final product fulfills its intended use in the real-world context. Here, human factors, user needs, and environmental conditions come into play—making usability testing and field trials critical components.
According to the FDA’s Quality System Regulation (21 CFR Part 820), both processes are mandated under FDA design controls and must be documented systematically. The agency differentiates the two because skipping one compromises not just product integrity but patient safety and public trust.
When teams merge these stages or skip ahead to validation without verifying design fidelity, the consequences can be steep, leading to failed audits or even product recalls.
In the next section, we’ll take a deeper dive into how these principles are applied in the medical device industry, where compliance is both science and strategy.
Basics of Design Verification & Design Validation Process
The design verification and validation process operates as a quality checkpoint system within product development, especially in regulated industries. Both stages are deeply rooted in identifying risks early and confirming product reliability under expected use conditions.
Verification Process:
- Initiated after design outputs are ready
- Uses defined test protocols (e.g., bench tests, CAD simulations, code reviews)
- Objective: Ensure each output matches input specs
Validation Process:
- Conducted on the final product version
- Involves real-world or simulated use
- Objective: Ensure the product performs as intended in user scenarios
Both require detailed documentation—test plans, execution records, review logs—all tied back to risk analysis.
Design controls and V&V are inseparable. Integrating them into a unified digital platform like Qualityze QMS minimizes data silos, ensures timely approvals, and improves compliance traceability.
Up next, let’s walk through smart, real-world tips to make your V&V process faster, leaner, and more inspection-ready.
Tips for Better Design Verification & Validation
Improving your design verification and validation process goes beyond regulatory compliance—it’s about delivering reliable, safe products that win user trust and pass audits confidently.
Here are proven tips to strengthen your V&V strategy:
- Begin V&V planning early: Avoid treating V&V as an end-of-cycle task. Build it into the design phase to detect flaws earlier.
- Write measurable design inputs: Vague requirements lead to unverifiable outputs. Each input should be specific, testable, and traceable.
- Use risk-based testing: Prioritize high-risk features for more rigorous verification and validation.
- Leverage cross-functional reviews: Involve QA, engineering, and regulatory teams to ensure robust test coverage.
- Automate traceability: Link requirements, test cases, and validation results using a QMS to minimize errors and omissions.
Qualityze offers a powerful QMS that embeds verification protocols, connects them with design controls, and simplifies audit readiness.
Now that we’ve discussed the “how,” let’s look at the “when” by exploring the steps to create effective verification and validation plans.
Steps to Create effective design verification and validation plans
An effective design verification and validation plan is not a one-size-fits-all checklist. It requires thoughtful planning, cross-functional input, and tight alignment with regulatory expectations.
Follow these strategic steps:
- Initiate with Regulatory Review
Start with understanding relevant standards like FDA 21 CFR Part 820 or ISO 13485 to scope your plan accordingly. - Map Requirements to Testing Methods
Connect every design requirement to a test method—this is the foundation of V&V traceability. - Create Risk-Driven Test Plans
Use your product’s risk profile to determine test rigor—high-risk items should undergo more intense validation. - Assign Deliverables and Ownership
Detail who will prepare protocols, run tests, approve results, and handle deviations. - Include Acceptance Criteria
Define pass/fail standards up front to avoid subjective interpretations during execution. - Digitize for Agility
Use QMS software to manage revisions, track approvals, and archive evidence.
Coming up: Let’s summarize the insights, explore how Qualityze can elevate your V&V, and guide you to your next actionable step.
Concluding thoughts!
In regulated industries, the cost of failing verification or validation can be severe—ranging from regulatory penalties to patient safety risks. This makes it critical to treat V&V not as one-time checks, but as integral components of your product development lifecycle.
Key Takeaways
✔ Design verification checks if the product is built right; validation ensures it's the right product
✔ Understanding FDA definitions helps align your processes with global standards
✔ Medical device manufacturers must conduct both V&V as per 21 CFR 820
✔ Effective planning, risk prioritization, and documentation are crucial to success
✔ Digital QMS solutions streamline traceability, reviews, and audit readiness
The Qualityze Advantage
Qualityze provides a purpose-built Quality Management Software that enables teams to plan, track, and manage all aspects of design verification and validation. From protocol management to traceability matrices and digital approvals, Qualityze helps you maintain compliance while improving time-to-market.
Ready to modernize your V&V process?
Request a personalized DEMO and see how Qualityze can power your product lifecycle success.
Share
The Start of Something Amazing.
Request Demo
Products
Industries